
샌드블라스팅 표면이 R245fa 흐름 비등 성능 향상에 미치는 영향 연구
Abstract
With the advancement of microelectronic technology and the continuous improvement of device integration, microelectronic devices’ power density and heat generation have continuously increased. As microelectronic devices generate high heat flux exceeding 150 W/cm2, we need a more efficient solution for thermal management. Flow boiling is a proper solution due to the high heat transfer coefficient, less coolant flow rate, and uniform temperature distribution across the channel surface. However, the plain surface of minichannel has a small number of nucleation sites; surface modification can be a promising solution for enhancing boiling. Sintering, electric discharge machining (EDM), chemical etching, and coating have been investigated for surface modification, but these methods require considerable time, have a lot of costs, and have low productivity. Sandblasting, a method that sprays small abrasives under high-pressure air, is suitable for industrial applications because of its high productivity. Therefore, this study analyzed flow boiling heat transfer enhancement by applying sandblasting on the heat transfer surface. The experimental results showed that the onset of nucleate boiling is triggered at a smaller wall superheat, and the heat transfer coefficient is enhanced by 127%. Visualization analysis further confirmed that a sandblasted surface generates more nucleation sites, and the distribution of the nucleation sites is more uniform compared to a plain surface. Additionally, flow boiling heat transfer increased as the sandblasting abrasive became larger, using a 0.6 mm SUS cut-wire, which had the best heat transfer performance among all test conditions.
Keywords:
Flow boiling, Minichannel, Sandblasting, Surface roughness, Heat transfer coefficient키워드:
흐름 비등, 미니 채널, 샌드블라스팅, 표면 조도, 열전달계수1. 서 론
최근 AI chipset의 급격한 발전과 전자/제어 장비의 고집적화 및 고성능화로 인해 전자장비의 크기는 감소하고, 단위 면적당 발생하는 열량은 크게 증가하고 있다(1). 하지만 기존의 냉각 방식인 공기 냉각 방식(공냉식)은 공기의 낮은 밀도와 비열에 의해 냉각 효과가 제한적이다. 또한 액체 냉각 방식(수냉식) 방법은 냉각 채널 내부의 온도 편차를 발생시키고 열응력을 발생시켜 전자장비의 열적 변형을 유발하는 내구성에 부정적인 영향을 초래할 수 있다는 단점을 가지고 있다. 이러한 한계를 극복하고 보다 효과적인 냉각 성능을 구현하기 위해 잠열을 활용한 냉각방식이 주목받고 있다(2). 온도 차에 의한 열전달을 기반으로 하는 현열 대신 상변화에 의한 잠열을 이용하면 고밀도 전자장비에서 발생하는 높은 열유속을 보다 효과적으로 관리할 수 있다. 특히 냉각 채널 내에서 작동 유체의 상변화를 이용한 흐름 비등(flow boiling)을 적용하면, 단상 유동에 비해 적은 유량으로도 높은 열전달계수를 확보할 수 있을 뿐만 아니라 채널 내 온도의 균일성을 유지할 수 있다(3). 이러한 장점을 바탕으로 다양한 냉각 분야에서 활용 가능성이 높아 냉각 채널에서 흐름 비등을 적용하기 위한 연구가 활발히 진행되고 있다.
하지만 냉각 채널의 매끈한 표면은 비등을 활성화 할 수 있는 핵 생성 지점(nucleation sites)이 부족하여 높은 벽 과열도(wall superheat)를 형성할 뿐만 아니라 버블이 불규칙적으로 성장하여 유체의 흐름을 방해하는 심각한 흐름 불안정성(flow instability)을 초래한다는 문제점이 있다(4,5). 이러한 문제점을 개선하고 흐름 비등 열전달 성능을 향상시키기 위한 방안으로 표면 개질 기술이 주목받고 있다. 표면 개질을 통해 채널 표면에 핵 생성 지점들을 균일하게 분포시켜 열전달계수를 증가시킬 수 있으며, 동시에 버블의 안정적인 성장을 유도하여 흐름 불안정성을 개선할 수 있다(6).
이러한 표면 개질 기술은 주로 구리 분말 소결(7-8), 구리 woven mesh 소결(9), 방전 가공(10), 화학적 코팅(11-12) 등 다양한 방법으로 연구되어 왔다. Sun et al.(7)은 구 형태의 구리 입자를 채널 표면에 소결하여 흐름 비등 실험을 진행하였다. 그 결과, 핵비등 개시(onset of nucleate boiling, ONB) 가 발생하는 벽 과열도가 약 7.4 K 감소하였으며 열전달계수가 7-10배 향상됨을 확인하였다. Semenic and You(8) 역시 마이크로 채널 표면에 구리 분말 소결을 진행하였으며, 실험 결과 열전달계수가 2.5∼2.7배 향상되고 임계 열유속(CHF)은 1.5∼2배 향상됨을 보였다. 또한 흐름 불안정성이 개선되어 기존에 발생하던 온도 차의 변화가 6℃에서 1℃ 이하로 감소하였다. 이처럼 표면에 분말 소결을 통해 마이크로 다공성 구조(microporous structure)를 형성할 수 있으며, 구조 내부의 공동(cavity)들이 다수의 핵 생성 지점을 제공하여 비등을 효과적으로 촉진할 수 있음을 여러 선행 연구에서 입증하였다. 이때 공동 크기에 따라 비등 성능 향상에 미치는 역할이 달라지게 된다. 일반적으로 큰 공동은 버블 탈출을 용이하게 하며, 작은 공동은 모세관 효과를 증가시켜 표면에 액체를 빠르게 재충전시킴으로써 CHF를 지연시키는 역할을 한다. He et al.(9)은 두 가지 크기의 공동이 공존할 수 있도록 구리 woven mesh를 소결하여 이중 다공성(bi-porous) 구조를 형성하였으며, 이를 통해 열전달계수가 2.37 배 향상되고 흐름 불안정성이 개선되어 입구 압력 편차가 43% 감소함을 확인하였다. 한편 Jones and Garimella(10)는 방전 가공을 통해 채널 표면의 조도를 변화시켜 표면에 재진입 공동(reentrant cavity)을 형성하였으며, 표면 조도 3.9 μm와 6.7 μm에서 각각 30%와 35%의 열전달계수 향상을 보였다. 또한 Khanikar et al.(11)은 채널에 카본 나노 튜브 코팅을 통해 81%의 CHF 향상을 보였으며, Wang et al.(12)은 실리콘 나노와이어 코팅을 통해 표면의 모세 관력을 향상시킴으로써 열전달계수와 CHF가 향상되는 것을 확인할 수 있었다.
이전 선행 연구에서 다양한 표면 개질 방법을 통해 흐름 비등 열전달 성능의 향상이 확인되었다지만, 해당 방법들은 공통적으로 표면 개질 과정에서 과도한 비용과 많은 시간이 소요되어 생산성 측면에서 한계를 보이며, 실제 산업에 적용하기에 제약이 따른다. 특히 소결 공정에는 고온 진공로, 화학적 코팅에는 플라즈마 증착 장비 등과 같이 금속 표면 개질을 위한 별도의 추가적인 기술과 고가의 장비들이 필요하다. 또한 나노구조 코팅의 경우 약한 구조로 인해 장기 신뢰성 관점에서 내구성에 명확한 한계를 보였다(11). 따라서 쉽게 실제 산업에 적용할 수 있도록 보다 적은 비용과 시간이 소요되고, 높은 내구성을 가지는 금속 표면 개질 기술이 필요한 것으로 판단된다.
샌드블라스팅(sandblasting)은 표면 개질을 해야 하는 모재에 연마재를 고압으로 분사하는 대표적인 표면 처리 공정으로, 주로 표면의 오염물질을 제거하거나 표면을 다듬는 등 금속 외관 표면처리를 위해 사용된다. 샌드블라스팅을 비등 표면에 적용하면 연마재의 물리적인 충격으로 발생한 공동 (cavity)들이 핵 생성 지점으로 작용하여 비등 열전달 성능을 향상시킬 수 있다. 실제로 샌드블라스팅을 풀비등(pool boiling) 표면에 적용함으로써 열전달 성능을 향상시키고자 하는 선행 연구들이 진행되었다(13-15). 샌드블라스팅은 다른 표면 개질 방법에 비해 매우 적은 시간과 비용으로 표면에 비등 촉진 구조를 형성할 수 있으며, 뛰어난 경제성과 생산성을 바탕으로 쉽게 실제 산업에 적용할 수 있다. 또한 별도의 코팅 공정 없이 연마재와 모재의 물리적인 충격으로 공동을 형성하기 때문에 장기간 사용하여도 구조적 강성이나 내구성에 대한 문제가 없다. Falsetti et al.(13)은 샌드블라스팅 표면의 풀비등 실험을 진행하였으며, 장시간 반복성 실험에도 성능 악화가 발생하지 않고 재현성이 확인되는 것을 보였다. 하지만 샌드블라스팅은 비등 촉진 표면을 형성하기 위해 주로 풀비등 연구에서만 집중되어 왔으며, 샌드블라스팅을 통해 흐름 비등 열전달 성능을 향상시키고자 하는 연구는 아직 진행되지 않았다.
따라서 본 연구에서는 샌드블라스팅 표면처리가 흐름 비등 열전달 성능 향상에 미치는 영향을 검토하였으며, 열전달 성능의 주된 판단 지표로 ONB가 발생하는 벽 과열도와 열전달계수를 비교 분석하였다. 또한 표면 조도에 따른 열전달 특성을 해석하기 위해 0.2, 0.4, 0.6 mm 세 가지 크기의 SUS 컷와이어 쇼트를 사용하여 표면처리를 진행하였으며, 샌드블라스팅 표면처리를 진행하지 않은 매끈한 표면 채널과 열전달 특성을 상호 비교하였다.
2. 실험 시편 제작
2.1 샌드블라스팅 표면처리
Fig. 1(a)는 채널 표면에서 수행된 샌드블라스팅 표면처리 공정의 개략도를 나타낸다. 노즐에서 4 bar의 압축 공기를 통해 샌드블라스팅 연마재를 표면에 분사하며, 연마재의 물리적인 충격에 의해 표면에 공동을 생성하여 표면 거칠기를 형성한다. 연마재로는 원기둥 형태의 SUS 컷와이어 쇼트를 사용하였으며, 직경 0.2 mm, 0.4 mm, 0.6 mm의 세 가지 크기를 적용하여 샌드블라스팅 표면처리를 진행하였다. 이때 사용된 SUS 컷와이어 쇼트를 광학 현미경을 사용하여 Fig. 1(b)에 나타내었다.
2.2 표면 조도 특성
Fig. 1(c)는 샌드블라스팅 표면처리를 진행한 채널 표면을 SEM으로 촬영한 이미지를 나타낸다. 구리 채널 표면에 약 수십 마이크로미터 크기의 공동이 형성된 것을 확인할 수 있으며, SUS 컷와이어 쇼트의 크기가 증가할수록 표면이 더 깊게 파이고 더 거친 표면을 형성하는 것을 확인하였다. 표면 조도 측정기 (Mitutoyo SJ-410)를 사용하여 채널 표면의 24 곳 에서 표면 조도를 측정한 결과, SUS 컷와이어 쇼트의 직경이 0.2, 0.4, 0.6 mm일 때 평균 표면 조도는 각각 2.493, 5.108, 7.989 μm로 나타났다. 또한 측정된 표면 조도의 표준편차는 각각 0.221, 0.301, 0.434 μm로 계산되었으며, 이는 샌드블라스팅 공정의 불균일한 특성에도 불구하고 비교적 균일한 표면 조도가 형성되었음을 보여준다. 또한 샌드블라스팅 표면처리를 하지 않은 Plain 채널의 표면 조도는 0.496 μm로 나타났다. 표면 조도 특성을 Table 1에 요약하여 나타내었다.
3. 실험 장치 및 방법
3.1 실험 장치
Fig. 2(a)는 흐름 비등 실험을 위한 전체 실험 장치의 개략도이다. 작동 유체인 냉매는 reservoir에 저장되며, reservoir 내부를 흐르는 냉각 코일의 냉각수 온도와 유량을 제어함으로써 냉매의 포화압력을 제어한다. 액체 상태의 냉매는 기어 펌프(Micropump GJ-N23.FF11S.A)를 통해 루프 내에서 순환하며, 펌프 하단부에는 accumulator를 설치하여 실험이 진행되는 동안 시스템의 압력을 안정적으로 유지할 수 있도록 하였다. 냉매는 필터를 통과하면서 불순물이 제거되며, 이후 코리올리 질량유량계(OVAL CA010L)를 통해 유량을 측정하였다. 또한 Test section에 진입하기 전, sub-cooler를 통해 test section 입구 조건을 적절하게 제어하였다. Test section을 통과한 후 이상 (two-phase) 상태의 냉매는 판형 열교환기에서 응축되어 순환 과정을 반복할 수 있도록 구성하였다. 또한 실험이 진행되지 않는 동안에도 루프 내부를 closed system으로 유지할 수 있도록 by-pass 루프를 설치하였다.
Fig. 2(b)는 test section의 단면도를 나타낸다. Test section은 6개의 카트리지 히터가 삽입된 구리 히팅 블럭을 통해 가열되며, 카트리지 히터에 전력을 공급하기 위해 DC 전원공급기(Keysight N8741A)를 사용하였다. 구리 블럭에서 채널까지 열이 균일하게 전달되도록 구리 블럭 상단부와 채널 바닥 면을 같은 크기로 설계하였으며, 구리 블럭과 채널 바닥면 사이에 접촉 열저항을 최소화하기 위해 써멀 그리스(Laird Tgrease 1500)를 도포하여 부착하였다. 또한, 열손실을 줄이기 위해 히팅 블럭을 감싸는 부분은 낮은 열전도율을 가지는 PEEK와 G10 Epoxy 재질로 제작되었다. 또한, Kim et al.(16)의 연구와 동일하게 PEEK 하우징의 inlet plenum과 outlet plenum은 1/4 원 형태로 설계하여 각 채널에서 유동이 균일하게 분배되도록 하였다. 채널 상단부에는 유리를 통해 유동을 가시화할 수 있도록 하였고, 진공도를 확보하고 작동 유체 누수를 방지하기 위해 채널과 PEEK 하우징 사이, 채널과 유리 사이에 Viton O-ring을 사용하여 체결하였다.
히팅 블럭에는 25 mm 간격으로 5개의 T 타입 열전대(Omega Engineering, TJ36)를 삽입하여 온도를 측정하였으며, inlet plenum과 outlet plenum에 각각 T 타입 열전대와 압력 센서(Omega Engineering, MMA030V5P1C5T4A4 CE)를 설치하여 채널 입출구의 온도와 압력을 측정하였다. 온도, 압력, 및 유량 데이터를 취득하기 위해 두 대의 데이터 처리 장치(NI, FD-11614, Keysight, DAQ970A)를 사용하였으며, 흐름 비등 현상의 가시화 분석을 위해 초고속 카메라(PHANTOM VEO440L-18G-M)를 사용하였다. 모든 측정 데이터는 LabVIEW 소프트웨어를 통해 실시간으로 모니터링 및 저장될 수 있도록 구성하였다.
3.2 실험 과정
작동유체로는 냉매 R245fa를 사용하였으며, 실험은 포화 온도 20℃ 조건에서 진행되었다. Test section 입구 온도는 15℃로 제어하였으며, 두 가지 질량 유속 조건(G = 211.2, 352.1 kg/m2s)에서 실험이 진행되었다.
실험에 앞서 불응축가스의 영향을 제거하기 위해 루프 내부의 진공도를 확보한 후 냉매를 충전하였다. 충전된 냉매는 순환펌프를 통해 루프를 순환하며, 니들 밸브를 통해 유량을 제어하였다. 구리 블록에 공급되는 열량은 카트리지 히터에 DC 전원공급기를 사용하여 50 W 씩 단계적으로 증가시키면서 공급하였다. 구리 블럭에서 측정한 온도 편차가 0.1℃ 이하일 때, 정상상태(steady-state)의 열전달 조건에 수렴한 것으로 확인하고, 다음 단계로 넘어가 단계적으로 열량을 증가시키면서 실험을 진행하였다. 실험은 재현성을 확인하기 위해 3회 반복 측정하였으며, 3회 진행된 실험 데이터의 평균값을 사용하여 결과를 분석하였다.
4. 데이터 처리 및 불확도 분석
4.1 Heat loss 측정
실험이 진행되는 동안 카트리지 히터로 공급한 전체 열원 중 plenum을 통한 전도 열전달, 주위로의 자연 대류 및 복사 열전달로 인한 heat loss가 발생하게 된다. 실제로 미니채널에서 작동유체에 전달되는 열을 계산하기 위해 test section의 heat loss를 측정하였다. Heat loss 측정은 작동유체가 공급되지 않은 빈 상태에서 구리 히팅 블럭에 열원을 공급하여 진행되었으며, 이때 작동유체가 없는 상태이기 때문에 공급한 열량이 식 (1)과 같이 모두 heat loss로 발생하게 된다.
(1) |
5 W 단위로 열량을 증가시키면서 구리 블럭의 온도와 주변 온도를 측정하였으며, 측정한 구리 블록 온도의 평균 Ttc,avg과 주변 온도 Tamb의 차에 대한 선형 관계를 식 (2)와 같이 도출하였다. 또한 온도 차에 대한 heat loss 관계를 Fig. 3에 나타내었다.
(2) |
해당 heat loss 측정 방법은 여러 선행 연구에서 사용되었으며, 충분한 정확도를 보임을 확인하였다(17-20).
4.2 데이터 처리
질량 유속은 작동유체의 질량유량 , 채널 수 Nch, 채널 단면 면적 Ach를 통해 식 (3)과 같이 계산되었다. 이때 채널 단면의 면적은 채널의 너비 Wch와 높이 Hch의 곱으로 Ach=Wch×Hch와 같이 계산된다.
(3) |
앞서 측정한 heat loss를 토대로 실제 채널에서 유체로 전달되는 유효 열량 Qeff과 유효 열유속 qeff은 각각 식 (4), (5)를 통해 계산되었다. 이때 채널 바닥 면적은 채널 전체 길이 Lhs와 채널 전체 너비 Whs의 곱으로 Ahs=Lhs×Whs와 같이 계산된다.
(4) |
(5) |
Test section 너비 방향의 단면을 Fig. 4에 나타내었다. 구리 블럭에서 열전대로 온도를 측정한 지점부터 채널 벽까지의 열전달은 일차원 열전도를 가정하였으며, 이를 기반으로 구리의 열전도율 kCu, 써멀 그리스의 열전도율 kgrease, 열전대를 통해 온도를 측정하는 지점부터 구리 블럭 상단부까지의 거리 H1, 써멀 그리스의 두께 Hgrease, 채널 바닥면부터 채널 벽까지의 거리 H2를 통해 식 (6)과 같이 국부적인 채널 벽 온도를 계산하였다. 이때 하첨자 i는 구리 블럭에서 온도 측정 위치를 나타내며, i = 1, 2, 3, 4, 5로 5개 지점으로 구성되어 있다.
(6) |
채널 사이의 벽은 핀과 같은 역할을 하기 때문에, 국부 열전달계수는 식 (7)과 같이 핀 효율 ηfin을 고려하여 계산하였다. 이때 채널 상단부에 낮은 열전도율을 가지는 유리가 위치하므로 핀 끝이 단열된 경우의 핀 효율을 나타내는 식 (8)을 사용하였으며, 핀 파라미터는 식 (9)를 통해 산출하였다.
(7) |
(8) |
(9) |
이때 Wfin은 채널 사이의 벽의 너비를 의미한다. 또한 작동유체의 온도 Tf,i는 냉매의 포화온도를 사용하였다. 국부 열전달계수 hi는 식 (7)-(9)을 이용하여 반복 계산을 통해 계산하였다.
증기 건도는 열역학적 평형을 통해 식 (10)과 같이 계산하였다. 이때 Ztc,i는 채널 입구로부터 열전대로 온도를 측정하는 위치까지의 거리, Tin은 inlet plenum에서 측정한 작동 유체의 온도이며 비열 cp,f과 잠열 hfg은 냉매의 포화압력 조건에서의 값을 사용하였다.
(10) |
5. 실험 결과
5.1 비등 곡선
매끈한 표면 채널(Plain)과 샌드블라스팅 표면처리를 진행한 채널(SBM)의 비등 곡선을 Fig. 5에 나타내었다. 이때 벽 과열도를 계산할 때 채널 출구와 가장 가까운 지점(Ttc,5)에서 측정한 온도를 사용하였다. 비등이 시작되면서 그래프의 기울기가 급격하게 변화하기 시작하는 지점을 ONB로 정의하였으며, G=211.2 kg/m2s와 G=352.1 kg/m2s 조건에서 모두 ONB가 발생할 때의 벽 과열도가 Plain에 비해 SBM에서 감소함을 확인하였다. 또한 표면 조도가 증가할수록 ONB가 발생하는 벽 과열도가 감소하는 경향을 보였다. G=211.2 kg/m2s 조건에서 ONB가 발생하는 벽 과열도가 Plain에서 8.5℃인 반면 SBM(0.6 mm)에서 3.9℃로 최대 4.6℃ 감소하였다. ONB가 발생하는 벽 과열도가 작을수록 더 적은 표면 온도를 통해 비등을 활성화할 수 있다는 것을 의미하며, 샌드블라스팅 표면이 핵 비등(nucleate boiling)을 효과적으로 촉진시킬 수 있음을 확인할 수 있다.
ONB가 발생할 때의 비등 메커니즘을 분석하기 위해 초고속 카메라를 통해 Plain과 SBM에서의 비등 특성을 비교하였다. ONB가 발생하는 qeff=22.1 kW/m2 조건에서 촬영한 비등 가시화 결과를 비교하여 Fig. 6에 나타내었다. Plain에서 촬영한 가시화 결과 Fig 6.(a)에서는 버블이 채널의 모서리에서 집중되어 발생하는 것을 확인할 수 있다. 또한 버블이 탈출한 후 급격하게 성장하여 버블 크기가 상대적으로 크며, 채널 전체적으로 버블 분포가 불균일한 것을 확인할 수 있다. 반면 SBM(0.6 mm)에서 촬영한 가시화 결과인 Fig 6.(b)에서는 버블이 채널 전체에서 균일하게 발생하며, 버블이 탈출한 후 안정적으로 성장하여 버블 크기가 상대적으로 작으며 채널 전체적으로 버블 분포가 균일한 것을 확인할 수 있다. 이는 샌드블라스팅을 통해 핵 생성 지점의 수가 증가할 뿐만 아니라 그 분포가 채널 표면에 균일하게 분포하여 버블들이 안정적으로 탈출하고 성장할 수 있는 환경을 제공할 수 있음을 보여준다. 실제로 비등 가시화 결과를 비교하면 Plain에서는 채널 모서리만 핵 생성 지점으로 작용하는 반면, SBM은 채널 바닥면 전체가 핵 생성 지점으로 작용하는 것을 확인할 수 있다.
5.2 열전달계수
Fig. 7(a)와 (b)는 각각 유효 열유속과 증기 건도에 따른 열전달계수 그래프이다. 일반적으로 열전달계수는 Plain과 SBM에서 모두 열유속과 증기 건도가 증가함에 따라 증가하는 경향을 보인다. 또한 Lee et al.(22)와 같이 비등이 시작될 때 열전달 메커니즘이 대류 열전달에서 핵 비등으로 천이함에 따라 작동 유체가 많은 양의 열을 흡수하여 열전달계수의 급격한 증가를 보이며, 핵 비등이 본격적으로 시작된 이후에는 열유속이 증가함에 따라 열전달계수가 완만하게 증가한다.
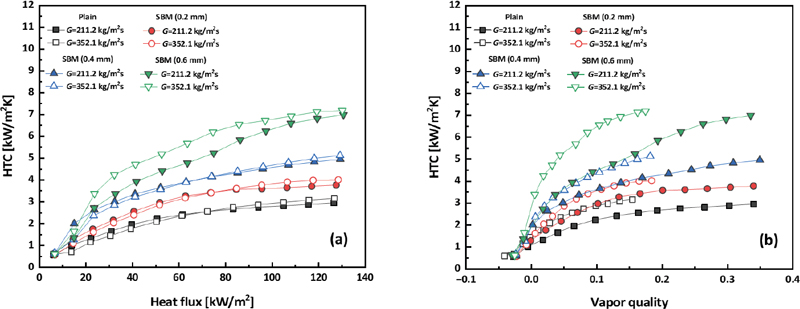
The heat transfer coefficients under different mass fluxes as function of : (a) effective heat flux and (b) vapor quality
본 실험에 사용된 작동 유체 R245fa는 포화 온도 20℃에서 194 kJ/kg의 잠열을 가지는 반면, 물은 2256 kJ/kg의 잠열을 가진다. 따라서 작동 유체로 물을 사용하여 흐름 비등 실험을 진행한 연구에서는 열전달계수가 105 W/m2K 수준으로 나타나는 반면(23-25), 본 실험 결과를 포함하여 작동 유체로 냉매를 사용하여 흐름 비등 실험을 진행한 연구에서는 열전달계수가 104 W/m2K 수준으로 나타나는 것을 확인할 수 있다. 또한 식 (12)와 같이 Cole and Rohsenow 상관식(26)을 이용하여 버블 탈출 직경을 계산한 결과, 작동 유체 R245fa의 작은 표면장력으로 인해 물과 비교하여 작은 버블 탈출 직경을 가지게 된다. 따라서 높은 증기 건도에서도 버블 유동이 슬러그류(slug flow)나 환상류(annular flow)로 천이되지 않고, 핵 비등 상태를 유지할 수 있다(27). 또한 액체 상태와 기체 상태의 밀도 차가 물에 비해 작기 때문에 높은 증기 건도에서도 열전달 성능이 크게 악화되지 않는다. 따라서 흐름 비등에서 작동 유체로 냉매를 사용하면 물에 비해 잠열이 작아 열전달계수는 작지만 높은 열유속과 높은 증기 건도 상태에서도 비교적 안정적으로 작동이 가능하다.
(12) |
Fig 7.(a)에서 확인할 수 있듯이 Plain에 비해 SBM에서 열전달계수가 상승하였으며, SBM에서는 연마재의 크기가 증가할수록 더 거친 표면 조도를 형성하여 열전달계수가 증가하는 경향성을 보인다. 가장 큰 열유속 조건인 126.9 kW/m2에서 최대 열전달계수가 발생하였으며, 해당 조건에서의 열전달계수를 비교하여 Fig. 8에 나타내었다. G = 352.1 kg/m2s 조건에서 Plain의 최대 열전달계수는 3.16 kW/m2K 로 나타난 반면, SBM 0.2, 0.4, 0.6 mm에서는 각각 4.19, 5.12, 7.17 kW/m2K로 나타났으며 최대 127% 상승함을 보였다. 이는 샌드블라스팅 표면처리를 통해 많은 수의 공동이 생성되어 핵 생성 지점이 증가하였을 뿐만 아니라 모세관력 향상으로 인하여 버블 탈출 빈도가 증가하여 비등 열전달 성능이 향상된 것으로 판단할 수 있다(14). 하지만 냉매의 큰 잠열로 인해 질량 유속에 의한 열전달계수의 의존성은 미미하였다. G = 211.2 kg/m2s에 비해 G = 352.1 kg/m2s에서 질량 유속이 증가함에 따라 대류 열전달 효과가 상승하여 낮은 벽 온도를 형성함에 따라 열전달계수가 조금씩 상승한 경향을 보이며, 이는 질량 유속이 증가할수록 열전달계수가 증가하는 경향을 보이는 He et al.(9)의 실험 결과와 일치함을 확인할 수 있다. 또한 Fig 7.(b)에서 G = 211.2 kg/m2s에 비해 G = 352.1 kg/m2s에서 더 적은 증기 건도를 보이는 것을 확인할 수 있고, 이것은 동일한 열유속을 가했을 때 질량 유속이 클수록 증기로의 상변화가 적게 발생하였기 때문이며, 질량 유속이 클수록 dryout을 지연시킬 수 있음을 알 수 있다.
6. 결 론
본 연구에서는 샌드블라스팅 표면처리를 통한 표면 거칠기가 흐름 비등 열전달 향상에 미치는 영향을 실험적으로 분석하였다. 표면 조도에 따른 흐름 비등 열전달 성능을 비교하기 위해 0.2, 0.4, 0.6 mm 세 가지 크기의 SUS 컷와이어 쇼트를 사용하여 샘플을 제작하였으며, 연마재 크기가 증가할수록 더 거친 표면을 형성하여 높은 표면 조도를 보이는 것을 확인하였다. 흐름 비등 열전달 성능을 판단하기 위해 ONB가 발생할 때의 벽 과열도와 열전달계수를 비교하였으며, 비등이 발생하는 유동 가시화를 통해 비등 메커니즘을 분석하였다. 본 연구의 주요 결론은 다음과 같다.
- 1) ONB가 발생하기 위한 벽 과열도가 Plain에 비해 SBM 에서 2.1∼4.6℃ 감소하였으며, 표면 조도가 증가할수록 감소하는 경향을 보였다. 샌드블라스팅 표면에서 발생한 많은 수의 핵 생성 지점으로 인해 핵 비등이 효과적으로 발생할 수 있는 환경을 제공하는 것을 확인할 수 있다.
- 2) ONB가 발생하는 22.1 kW/m2 조건에서 흐름 비등의 유동 가시화 특성을 비교하였다. Plain에 비해 SBM에서 버블 크기가 상대적으로 작으며 채널 바닥면에서 균일하게 버블이 탈출하는 것을 확인하였다. 샌드블라스팅 표면이 버블들이 보다 안정적으로 탈출하고 성장할 수 있는 환경을 제공함을 확인하였다.
- 3) 최대 열전달계수의 경우 G = 352.1 kg/m2s에서 Plain이 3.16 kW/m2K, SBM(0.6 mm)에서 7.17 kW/m2K로 약 127% 상승하였다. 샌드블라스팅을 통해 많은 수의 핵 생성 지점을 제공하고 모세관력 향상으로 인해 버블 탈출 빈도가 증가함으로써 연마재 크기가 증가할수록 열전달계수가 증가하는 경향을 보였다.
따라서 본 연구를 통해 샌드블라스팅 표면처리로 흐름 비등 성능을 효과적으로 향상시킬 수 있음을 보였다. 샌드블라스팅 공정의 우수한 생산성과 내구성을 바탕으로 향후 고밀도/고발열 전자장비 냉각을 위한 표면 개질 방법에 적용할 수 있을 것으로 기대한다.
Acknowledgments
본 연구는 ㈜현대로템의 산학협력 연구지원을 통해 수행되었으며, 이에 감사드립니다.
References
-
Zhang, Zhihao, Xuehui Wang, and Yuying Yan, 2021, “A Review of the State-of-the-Art in Electronic Cooling,” E-Prime - Advances in Electrical Engineering, Electronics and Energy, Vol. 1, 100009.
[https://doi.org/10.1016/j.prime.2021.100009]
-
Mudawar, I. (2013). Recent advances in high-flux, twophase thermal management.Journal of Thermal Science and Engineering Applications,5(2), 021012.
[https://doi.org/10.1115/1.4023599]
-
Karayiannis, T. G., & Mahmoud, M. M. (2017). Flow boiling in microchannels: Fundamentals and applications. Applied Thermal Engineering, 115, 1372-1397.
[https://doi.org/10.1016/j.applthermaleng.2016.08.063]
-
Zhang, L., Wang, E. N., Goodson, K. E., & Kenny, T. W. (2005). Phase change phenomena in silicon microchannels. International journal of heat and mass transfer, 48(8), 1572-1582.
[https://doi.org/10.1016/j.ijheatmasstransfer.2004.09.048]
-
Wu, H. Y., & Cheng, P. (2004). Boiling instability in parallel silicon microchannels at different heat flux.International Journal of Heat and Mass Transfer, 47(17-18), 3631-3641.
[https://doi.org/10.1016/j.ijheatmasstransfer.2004.04.012]
-
Liang, G., & Mudawar, I. (2020). Review of channel flow boiling enhancement by surface modification, and instability suppression schemes. International Journal of Heat and Mass Transfer, 146, 118864.
[https://doi.org/10.1016/j.ijheatmasstransfer.2019.118864]
-
Sun, Y., Zhang, L., Xu, H., & Zhong, X. (2011). Flow boiling enhancement of FC-72 from microporous surfaces in minichannels. Experimental thermal and fluid science, 35(7), 1418-1426.
[https://doi.org/10.1016/j.expthermflusci.2011.05.010]
-
Semenic, T., & You, S. M. (2013). Two-phase heat sinks with microporous coating. Heat transfer engineering, 34(2-3), 246-257.
[https://doi.org/10.1080/01457632.2013.703572]
-
He, B., Luo, X., Yu, F., Zhou, J., & Zhang, J. (2020). Flow boiling characteristics in bi-porous minichannel heat sink sintered with copper woven tape.International Journal of Heat and Mass Transfer, 158, 119988.
[https://doi.org/10.1016/j.ijheatmasstransfer.2020.119988]
-
Jones, B. J., & Garimella, S. V. (2009). Surface roughness effects on flow boiling in microchannels.
[https://doi.org/10.1115/1.4001804]
-
Khanikar, V., Mudawar, I., & Fisher, T. (2009). Effects of carbon nanotube coating on flow boiling in a micro-channel. International Journal of Heat and Mass Transfer, 52(15-16), 3805-3817.
[https://doi.org/10.1016/j.ijheatmasstransfer.2009.02.007]
-
Wang, S., Chen, H. H., & Chen, C. L. (2019). Enhanced flow boiling in silicon nanowire-coated manifold microchannels. Applied Thermal Engineering, 148, 1043-1057.
[https://doi.org/10.1016/j.applthermaleng.2018.11.125]
-
Falsetti, C., Chetwynd-Chatwin, J., & Walsh, E. J. (2024). Pool boiling heat transfer of Novec 649 on sandblasted surfaces. International Journal of Thermofluids, 22, 100615.
[https://doi.org/10.1016/j.ijft.2024.100615]
-
Song, Y., Wang, C., Preston, D. J., Su, G., Rahman, M. M., Cha, H., ... & Wang, E. N. (2022). Enhancement of boiling with scalable sandblasted surfaces. ACS Applied Materials & Interfaces, 14(7), 9788-9794.
[https://doi.org/10.1021/acsami.1c22207]
-
Lin, L., Hu, Y., Zhu, M., Su, Z., Liu, K., Fan, C., & Huang, J. (2022). Boiling heat transfer on the micro-nano structured surface fabricated by mechanical sandblasting/alkali-assisted oxidation. International Journal of Heat and Mass Transfer, 183, 122079.
[https://doi.org/10.1016/j.ijheatmasstransfer.2021.122079]
-
Kim, H. G., Shah, Y., & Kim, S. M. (2023). Experimental investigation and analysis of two-phase flow instability of flow boiling in a mini-channel heat sink. International Journal of Heat and Mass Transfer, 213, 124309.
[https://doi.org/10.1016/j.ijheatmasstransfer.2023.124309]
-
Zhang, Z., Wu, Y., He, K., & Yan, X. (2024). Experimental investigation into flow boiling heat transfer and pressure drop in porous coated microchannels. International Journal of Heat and Mass Transfer, 218, 124734.
[https://doi.org/10.1016/j.ijheatmasstransfer.2023.124734]
-
Mathew, J., Lee, P. S., Wu, T., & Yap, C. R. (2019). Experimental study of flow boiling in a hybrid microchannel-microgap heat sink. International Journal of Heat and Mass Transfer, 135, 1167-1191.
[https://doi.org/10.1016/j.ijheatmasstransfer.2019.02.033]
-
Law, M., Lee, P. S., & Balasubramanian, K. (2014). Experimental investigation of flow boiling heat transfer in novel oblique-finned microchannels. International Journal of Heat and Mass Transfer, 76, 419-431.
[https://doi.org/10.1016/j.ijheatmasstransfer.2014.04.045]
-
Lee, P. S., & Garimella, S. V. (2008). Saturated flow boiling heat transfer and pressure drop in silicon microchannel arrays. International Journal of Heat and Mass Transfer, 51(3-4), 789-806.
[https://doi.org/10.1016/j.ijheatmasstransfer.2007.04.019]
-
Moffat, R. J. (1988). Describing the uncertainties in experimental results. Experimental thermal and fluid science, 1(1), 3-17.
[https://doi.org/10.1016/0894-1777(88)90043-X]
-
Lee, J., & Mudawar, I. (2008). Fluid flow and heat transfer characteristics of low temperature two-phase micro-channel heat sinks–Part 2. Subcooled boiling pressure drop and heat transfer. International Journal of Heat and Mass Transfer, 51(17-18), 4327-4341.
[https://doi.org/10.1016/j.ijheatmasstransfer.2008.02.013]
-
Lan, Y., Feng, Z., Hu, Z., Zheng, S., Zhou, J., Zhang, Y., ... & Lu, W. (2023). Experimental investigation on the effects of swirling flow on flow boiling heat transfer and instability in a minichannel heat sink. Applied Thermal Engineering, 219, 119512.
[https://doi.org/10.1016/j.applthermaleng.2022.119512]
-
Yin, L., Jiang, P., Xu, R., Hu, H., & Jia, L. (2019). Heat transfer and pressure drop characteristics of water flow boiling in open microchannels. International Journal of Heat and Mass Transfer, 137, 204-215.
[https://doi.org/10.1016/j.ijheatmasstransfer.2019.03.108]
-
Benam, B. P., Sadaghiani, A. K., Yağcı, V., Parlak, M., Sefiane, K., & Koşar, A. (2021). Review on high heat flux flow boiling of refrigerants and water for electronics cooling. International Journal of Heat and Mass Transfer, 180, 121787.
[https://doi.org/10.1016/j.ijheatmasstransfer.2021.121787]
- R. Cole, & W.M. Rohsenow. (1969). Correlation of bubble departure diameters for boiling of saturated liquids. In: Chem Eng Prog Symp Ser, 211–213.
-
Qu, W., & Mudawar, I. (2003). Flow boiling heat transfer in two-phase micro-channel heat sinks––I. Experimental investigation and assessment of correlation methods. International journal of heat and mass transfer, 46(15), 2755-2771.
[https://doi.org/10.1016/S0017-9310(03)00041-3]